PM728 Bench Mill CNC Conversion
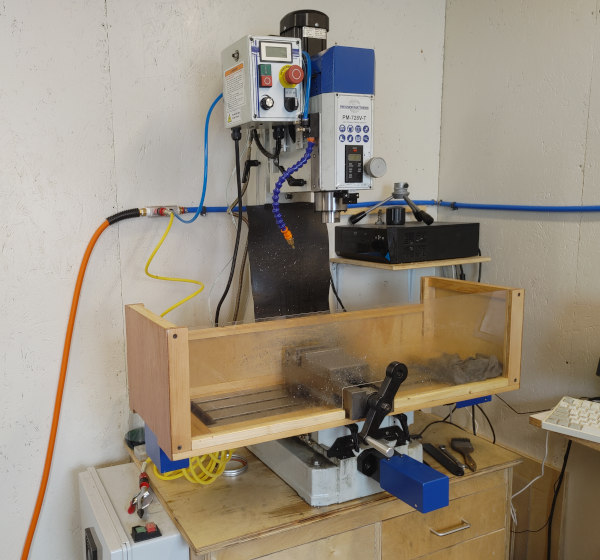
In 2020 I started the conversion of a Precision Matthews bench mill to CNC. This machine is for the winter shop in Brenda, AZ. Space is tight so a small bench mill is all that would fit.
I chose the Precision Matthews PM728 for the conversion. It is a small, 7"x28" table, mill from Taiwan. Better quality than the available Chinese machines, but not up to German or Swiss quality. Also at a price between these options, but closer to the Chinese. A nice machine.
Precision Matthews also offers a ball screw conversion kit for this mill. It supplies the ball screws and mounting hardware, but no motors or electronics. This makes the conversion much simpler and is the direction I took. I used NEMA 23 stepper motors on the X and Y, 425 oz-in and a NEMA 34 for the Z, 920 oz-in. All three steppers from Automation Technology.
The electronics are shown below. Very similar to my PM1022 conversion I used Mesa 7I76 and 5I25 cards and four Gecko G201X stepper drivers. I had the same problems as with the PM1022 conversion finding a computer with a PCI interface. The PCI seems to be antiquated. The four Geckos provide for axes X/Y/Z along with a rotational A axis. I haven't built the A axis yet but provided for it in the control. There is a relay board above the 7I76 card. It currently isn't connected but will be used for coolant, etc. A bank of fuses below the Gecko drives protect those drivers. Finally, a power supply from AnTek (PS-10N70N24R12) is on the left. It provides up to 14A at 70VDC for the steppers. This supply also gives 5VDC and 12VDC at 1A each of regulated output. The 12V output is used to supply the Field Voltage to the 7I76.
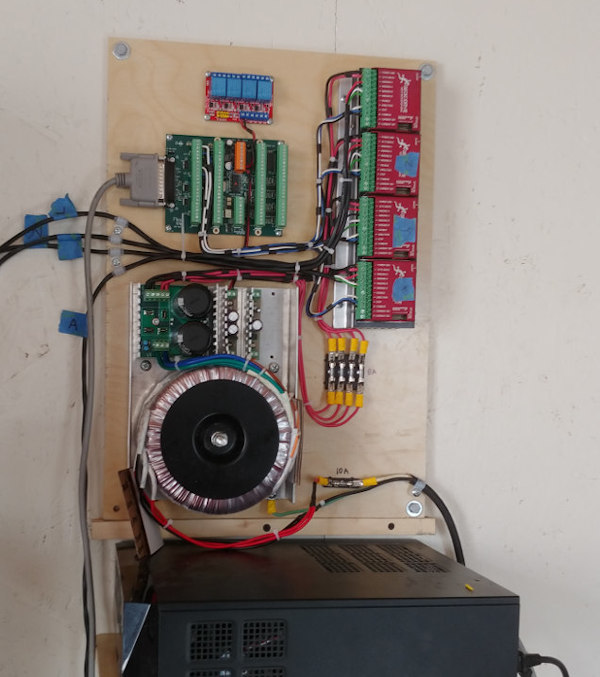
The electronics were put in a control box and mounted on the left end of the mill stand. The only addition to the controls shown is a latching on/off switch on the top. As with my PM1022 conversion slots are cut in the bottom of the control box with a cooling fan on the front. It can be seen in the first picture above.
An open enclosure was built on top of the milling table. It takes up less space than a full enclosure but still captures most chips. Mist coolant is used so a wooden enclosure box, well coated with polyurethane, is adequate. A polycarbonate window slides into the front while plywood "panels" of various sized slide into the back. This allows adjusting height of the back wall as the job changes. The picture at the top of the page best shows this enclosure box. If space is required beyond the table the box can easily be removed.
The enclosure box interferes with the stock PM728 control box. To solve this problem the box was raised some 6" as can be seen below.
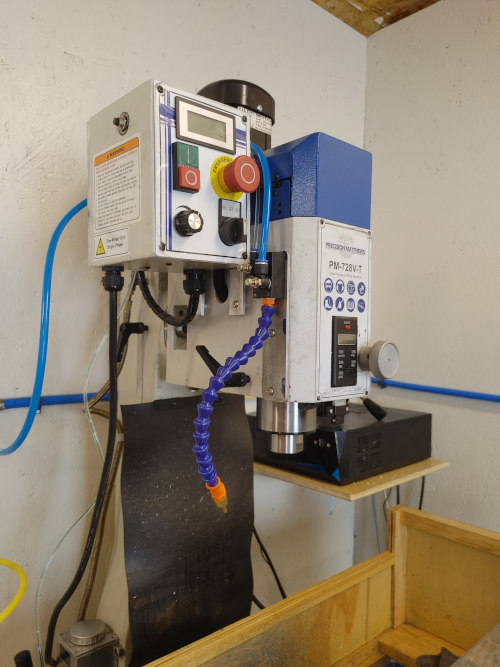
The vice shown in the first picture is a 4" CNC vice from Tormach. It's a nice vice for the price, no complaints. It would be nice if it was a little smaller in height, but the PM728 seems to have a lot of Z travel. I would like to find, or may have to build, a smaller speed handle for it.
This machine is working well. It is a small machine and this must be taken into account when planning cuts. I've added a mist coolant system as has always been the plan. I haven't added limit or home switches. These may be added later but not having them, on a hobby machine, isn't much of a problem.